Data analysis in manufacturing: how one company reduced operational costs by 12%
- Karolina Dyrla-Mularczyk
- May 19
- 2 min read
Data analysis in manufacturing – goals and challenges
Manufacturing operations generate massive volumes of data – energy usage, machine downtime, production waste. But for many companies, this data lives in spreadsheets and rarely gets analyzed. That was the case for our client: a mid-sized industrial manufacturer.
They reached out to us because they needed a centralized dashboard to track performance in real time – not by gut feeling.
The problem: scattered data and reactive decision-making
Data came from Excel, CSV files, even manual notes. Reports were built manually and often arrived too late to fix anything.
The solution: a Shiny dashboard for data analysis in manufacturing
We built a dashboard in R + Shiny that integrates data from all sources and shows:
energy usage per shift and line,
daily downtime in minutes,
waste by product type,
performance comparison between operators and shifts.
Everything is in one place – clean, fast, and live.
Results: 12% operational cost savings
After just 3 months:
energy usage decreased by 7%,
production waste dropped by 15%,
average daily downtime was reduced by 18 minutes,
total cost reduction: 12%..
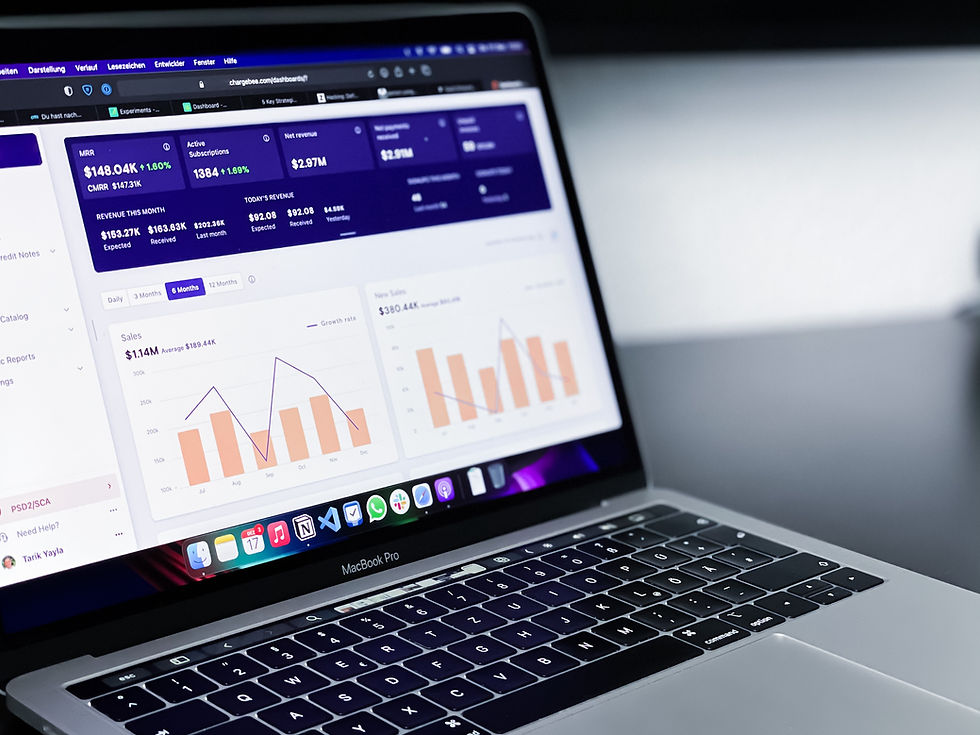
Implementing data analysis allowed this company to take full control of their production process and make decisions based on real-time insights instead of assumptions. Thanks to a custom dashboard built in R and Shiny, they turned raw data into meaningful improvements and measurable cost savings. If you're wondering how data analysis could improve your operations — let's talk. We specialize in turning data into real business outcomes.
Curious how data analysis could work for your company? Write to us at kontakt@stat.haus or book a short consultation.